Housebuilder Croudace Homes has been specifying Posi-Joist exclusively in its residential developments for 15 years, adopting the technology well ahead of the current demand for the joists in the UK market.
Founded in 1946, Croudace Homes is a five-star residential developer with a strong presence across the South East of England. One of the most respected private housebuilders in the UK, developing high-quality builds with a strong design aesthetic and a high specification of materials, the company prides itself on its passion, expertise and commitment to going the extra mile.
Having reaped the benefits of Posi-Joist for more than a decade, our colleagues at MiTek UK & Ireland caught up with the Croudace Homes team to find out why the joists form such an integral part of its high-end developments.
Setting the standard in homebuilding
Firstly, the floor joists are made offsite and arrive ready to be installed, meaning a safer, far more efficient way of working, as well as offering Croudace Homes the level of consistency and quality which sets them apart. Posi-Joist is also much more versatile than other products on the market.
“One of our main priorities is quality,” says Matthew McCourt, Site Manager at Croudace Homes.
“Posi-Joist has good dimensional stability so they’re a lot less susceptible to twisting and warping. They have good span capabilities which allows us to plan the layout of our homes better, so we can have more open-plan living.
“They’re much more adaptable than I-joists. When it comes to the first fix stage inside the property, Posi-Joists are much easier to work with. The electrician and the plumber find it much easier to run their cabling and pipe work through. And we know it saves time.”
Collaboration sits at the heart of what Croudace do. Working on site, different professionals from a range of trades need to do their jobs as quickly and efficiently as possible. Posi-Joist is streamlining the process, going so far as to provide clear zones for each trade’s input. There’s no potential for services to clash over space.
Trades are saving about a day or two of installation time each. That translates to incredible time and labour cost savings across a whole development.
Supply chain partners who worked on a recent project for Croudace, Firethorn Place in Surrey, less than 40 miles outside of London, spoke of the benefits their respective trades get from working with Posi-Joist:
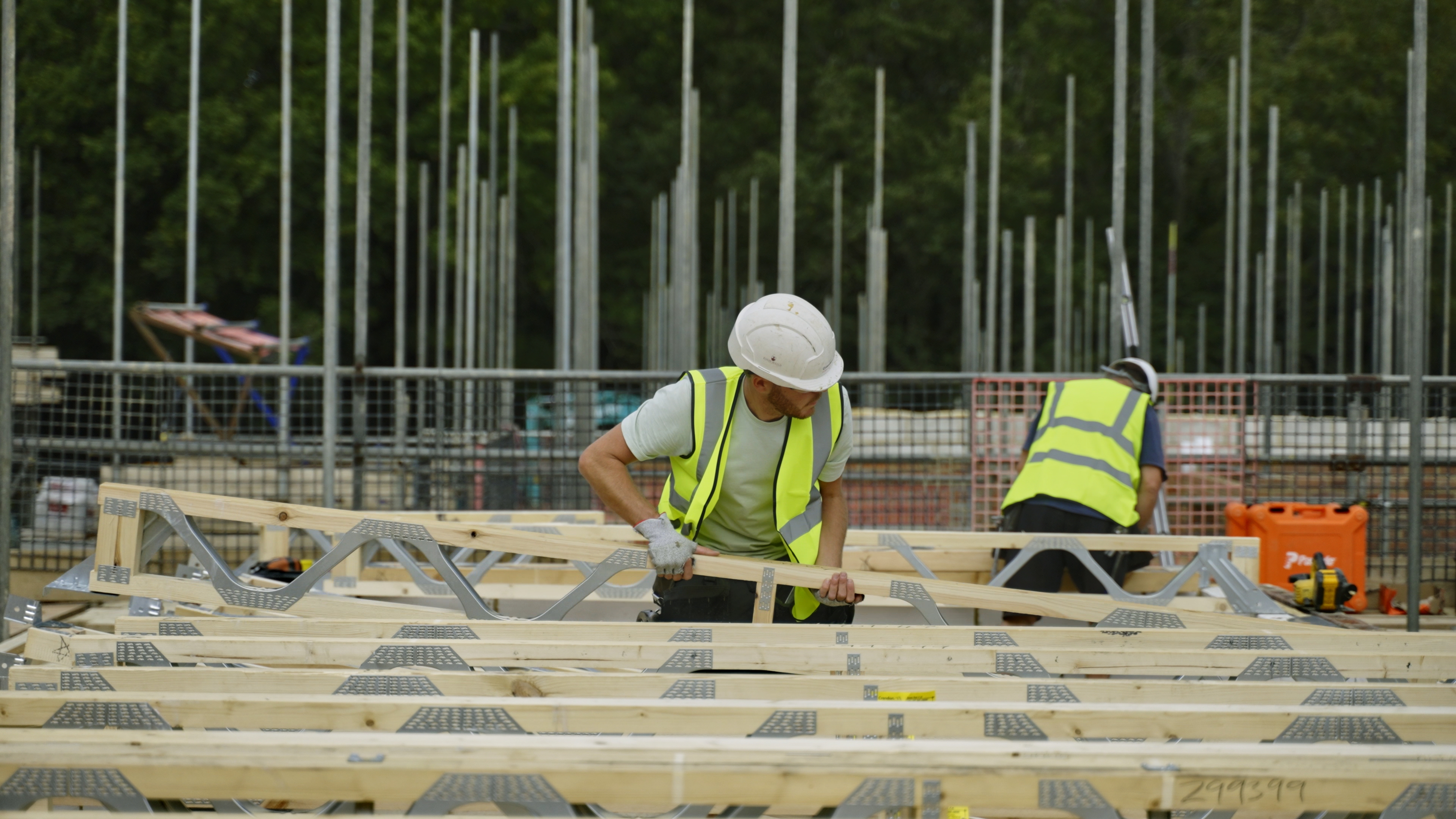
Mike Armstrong, SCC Carpentry
Mike has been using Posi-Joist for 15 years. It’s a lighter, more manageable solution compared to traditional joists. Components arrive prefabricated, ready to be placed.
To Mike, that’s huge: “Posi-Joist saves around two days of labour per installation. Obviously, that’s quite significant compared to old-style joists, but Posi is also straighter; there’s less movement. They’re easier to store safely, too. It’s a better-engineered solution all round.
“In fact, it’s the best joisting system on the market right now; I’d put it in my own house if I had the option. The Posi market can only grow and grow from here. Other trades who follow on from us, plumbers and electricians, maybe see even more benefits than we do.”
Sam Edwards, Goring Electricals
Sam has been using Posi-Joist for 10 years. He says: “With an old I-Beam or regular joist, there’s a lot more labour involved. You’ve got to drill out space for things, so you’re producing waste on site. Where does it go? There’s a potential safety concern. Meanwhile, everyone else is doing the same thing so you might end up competing for space.
“Compare that to a nice Posi-Joist. There’s plenty of room for everyone to work with it. We can run our cables straight through, or tie them if they’re parallel to the joist. When the guys come in and see we’re using it, they’re generally a bit happier.
“So, there’s three big benefits; it’s easier, you save time, and you can work together more easily with people doing other jobs.”
Dan Sanders, PRS Plumbing
Dan said: “I can get long lengths of pipe through less fitting using Posi-Joist. It works more flexibly; in the real world, you’re never going to be able to match the design 100% all the time. Posi lets us adapt, with less drilling, and still keep pipework together neatly. We don’t step on anyone’s toes when we’re using it.
“I’ve heard people look at the upfront costs and get cold feet. I’d advise them to think about what they’re saving in labour costs, time, wastage, and so on. It’s not only a compliance thing, we’re talking about a sound investment that makes life easier for everyone on site. That’s been my experience.”
Collaborate, conceive, construct: rethinking UK property
Construction in the UK is also facing the mandatory Future Homes Standard compliance for new builds. These regulations will ensure that UK homes will produce 75-80% less carbon, and help the UK achieve its 2050 net zero target. MiTek UK & Ireland is working closely with industry to drive sustainable, efficient design.
Partnerships, like with Croudace Homes, are helping get the best components in the hands of the best-qualified people. The result will be better, more sustainable housing for the UK, and we’re proud of the role our MiTek colleagues are playing in building that future.